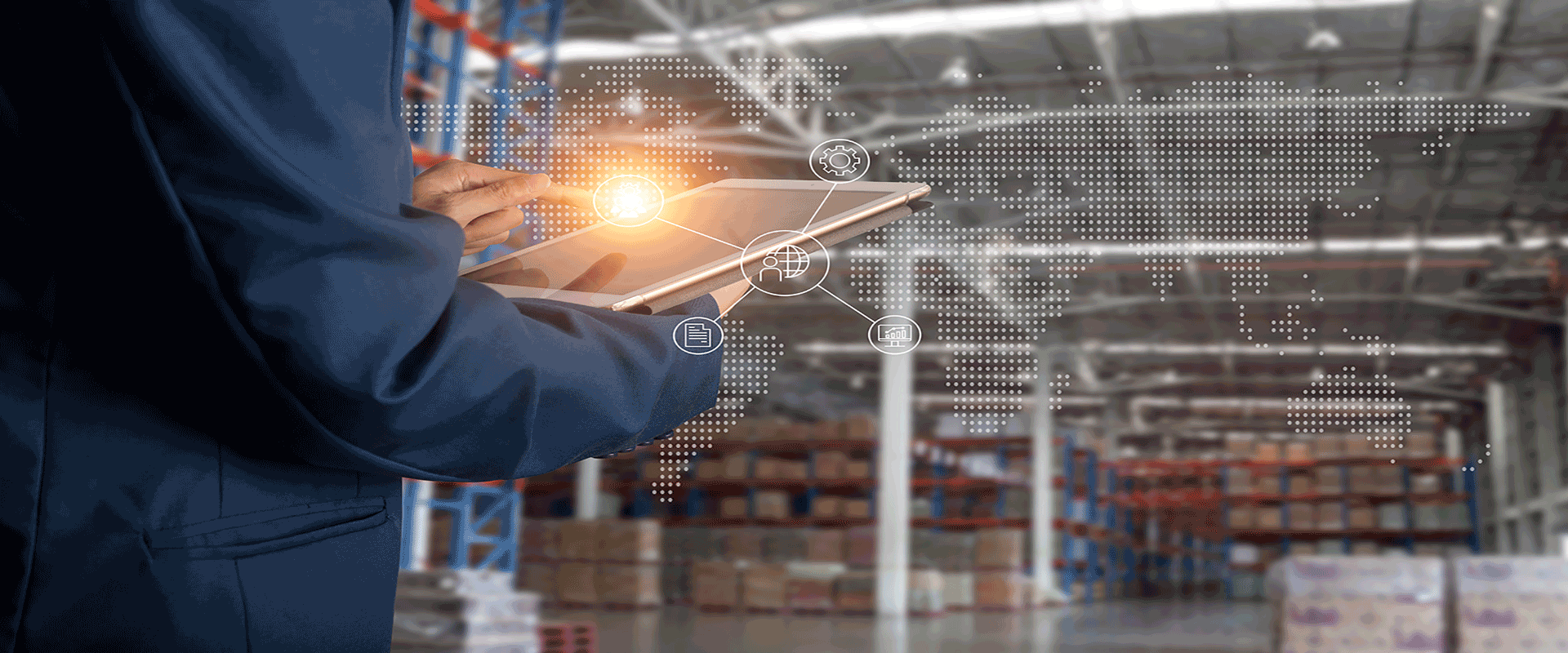
How Can Industrial Managers Best Navigate a Post-Pandemic World?
- Volume XXII, Issue 37
- Executive Insights
Industrial managers have started to emerge from COVID-19-related operational crisis management mode and are strategically thinking about the potential longer-term impacts.
While some uncertainty still remains about what the new normal will look like as industrial companies continue to adapt, we’ve identified several key themes to date.
Hygiene and safety measures are top of mind for industrial managers across end markets, with a focus on developing clear safety strategies to protect their workforce and meet changing customer needs.
Acceleration of digital initiatives will likely continue as companies seek more effective digital ways of working and engaging with suppliers and customers.
Regional/local supply chains that offer manufacturers operating flexibility are increasingly important for mitigating supply chain disruptions.
COVID-19 has led many industrial companies to change the way they operate. From increased safety measures for working staff to enhanced use of digital tools and platforms to reevaluation of supply chains, few areas have escaped being impacted by the COVID-19 pandemic. As industrial companies shift their focus from near-term survival to what the future looks like after the pandemic, industrial purchasing managers are now thinking about how their businesses are likely to operate differently by 2021 and beyond.
While COVID-19 has the potential to bring about profound macro changes in the way business is conducted moving forward, this Executive Insights focuses on the top themes that industrial managers have identified to date. Leveraging key findings from L.E.K. Consulting’s 2020 U.S. Industrial Managers Survey, we have focused on how industrial managers expect the new normal will look following the COVID-19 pandemic and the implications for industrial companies.
L.E.K.’s 2020 U.S. Industrial Managers Survey is a series of questionnaires conducted biweekly in order to measure COVID-19’s impact on the business outlook of U.S. industrial companies. The survey panel is composed of 120 executives at major U.S.-based industrial companies, and respondents come from businesses of varying industries, sizes and geographic reach (see Figure 1).
In the April 16 edition of L.E.K.’s U.S. Industrial Managers Survey, respondents were asked the extent to which they expect COVID-19 to lead to long-term changes within their industries into 2021 and beyond. Participants ranked each industry change on a scale of 1 to 7, with 7 indicating a strong expectation for the change to occur in the long term and 1 indicating the opposite sentiment. Figure 2 shows the changes that were most expected to occur in the long term and the share of respondents who “strongly” or “somewhat” (as indicated by a score of 6 or 7) expect the change to occur across five industrial end markets (building and construction, packaging, industrial parts and equipment, chemicals, and automotive).
Figure 2
Share of industrial purchasing managers who predict changes from 2021 on*
Source: L.E.K. U.S. Industrial Managers Survey (April 16, 2020)
*Survey question: What share of industrial purchasing managers report that they ‘strongly’ or ‘somewhat’ expect COVID-19 to lead to the following changes from 2021 on?
Industrial purchasing managers indicated that they expect three key themes to emerge on the back of COVID-19:
While it is not surprising that the health and safety of the workforce is top of mind for industrial businesses in the near term, these measures are also expected to have a long-lasting impact, with workplace safety being a major priority longer term (2021 and beyond). Across the five different industrial end markets, managers indicated that they expect COVID-19 to lead to increased hygiene and safety measures on both an operational and product level, with almost 70% of respondents “strongly” or “somewhat” expecting to change their adoption of hygiene and safety measures through the end of 2020 and beyond (see Figure 3).
Across industrial subsectors, companies are establishing hygiene and safety measures to address issues today and to prepare for a new normal:
Post-COVID-19, a clearly articulated safety strategy is likely to be ingrained in day-to-day operations as part of the new normal for industrial businesses. A renewed focus on equipping workforce with PPE, monitoring health on the job site (e.g., temperature checkpoints) and data tracking/analysis to be able to proactively address health and safety concerns will take on added importance even postcrisis as companies seek to manage any future complications. Ultimately those companies that reevaluate safety processes, develop best practices around actionable data and embrace change will best adapt to the new normal.
Across subsectors, industrial purchasing managers indicate that COVID-19 is bringing more attention to the strategic value of digital tools and solutions. In the long term (2021+), they expect COVID-19 to drive greater use and faster adoption of digital tools and solutions:
The emergence of COVID-19 has served as an inflection point in the adoption of digital ways of working, highlighting the value of digital productivity tools (e.g., videoconferencing, digital sales).
COVID-19 has brought into sharper focus a host of potential digital needs (e.g., remote servicing/diagnostics, online customer service and touchpoints); meeting those needs can help address immediate and longer-term challenges facing firms. Digital initiatives that previously may have been “nice-to-haves” are increasingly necessary for competitive advantage as commercial objectives are even more acute for industrials firms in lean times (see Figure 4). Additionally, maintaining cybersecurity across all the expanded digital tools remains critical.
Early adoption of digital tools and solutions has been seen across subsectors in response to COVID-19:
The conditions created by the pandemic have elevated the need for digital tools and solutions; they have even driven some industrial companies to accelerate their use of digital tools and solutions in the short term. While the new normal will not entirely replace the need for in-person customer experiences and ways of working, it will alter the way in which industrial firms leverage data-driven insights and digital capabilities to better serve their customers.
COVID-19 has caused supply chain disruptions for many industrial companies. According to the Institute for Supply Management, approximately 80% of companies expect to experience some disruption related to COVID-19, with roughly 60% of companies seeing worsening lead times since late 2019. In L.E.K.’s April 16 survey of industrial purchasing managers, some 62% of respondents indicated that the outlook for their business’s ability to access required supplies and materials over the next month had worsened.
In the past, many industrial companies have offshored key portions of their supply chain and are reliant on those suppliers to be able to meet demand. COVID-19 has led managers to reassess their supply chain architecture, with more than 45% of respondents “strongly” or “somewhat” anticipating a shift toward more regional/domestic supply chains, particularly within the packaging and industrial parts and equipment sectors (see Figure 5).
The effects of COVID-19 on supply chains have manifested themselves differently across industrial industries, with the greatest impact on industries and companies that have not already established strong regional/local supply chains:
COVID-19 has highlighted the need for companies to create more flexible supply chains that reduce the dependency on any single supplier or region. Incorporating contingency planning and greater regional diversity can help offset supply chain risk.
COVID-19 will lead to fundamental changes in the ways that industrial companies operate in whatever the new normal looks like within their industry. While some of these changes are expected to come with challenges, there will also be new opportunities created. To continue the discussion, please don’t hesitate to contact us.