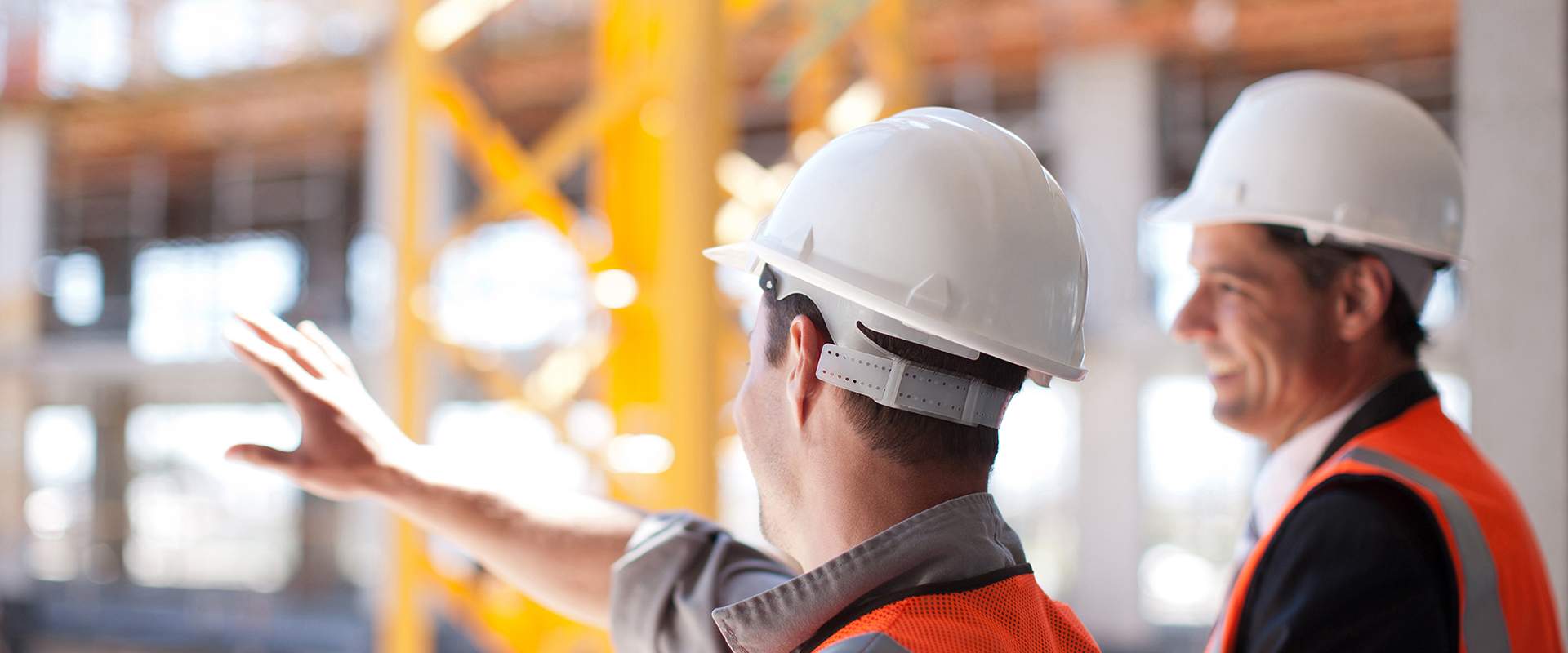
How Are Manufacturers Outsmarting the Construction Labor Shortage?
- Volume XXI, Issue 65
- Executive Insights
The U.S. construction industry is booming and job openings are abundant, but hiring is struggling to keep up.
This situation is creating long-term challenges for builders and contractors to fulfill demand and complete projects on schedule.
However, some manufacturers have capitalized on the upside of the labor shortage by developing products that decrease installation time, require fewer and/or less-skilled workers, and employ emerging technology.
In this Executive Insights, we examine what’s driving the labor shortage and discuss how time-saving and efficiency-boosting products are enabling companies to succeed in the current labor environment.
The U.S. construction industry is thriving, and the number of job openings continues to surge due to demand. But builders and contractors are wrestling with a profound problem: Where are the workers? With 2019 job openings reaching the highest levels since the U.S. Bureau of Labor Statistics started reporting these numbers in 2000, hiring is struggling to keep up.
Unfortunately, the tightening labor market is real — and it’s here to stay, creating long-term challenges for builders and contractors to fulfill demand and complete projects on schedule. However, some manufacturers are finding ways to address this issue through more innovative products, which are able to save time on labor and maximize efficiency. The manufacturers doing these things — and doing them right — will be best-positioned to win in the current labor environment.
In this Executive Insights, we discuss the forces driving the labor shortage and how it’s affecting contractors, builders and consumers alike. We also focus on how manufacturers have capitalized on the upside of the labor shortage by developing products that decrease installation time, require fewer and/or less-skilled workers, and employ emerging technology, to name a few.
2018 closed out with a bang in terms of available construction work, with job openings increasing to a cycle high of 312,000 in December. And this momentum carried into 2019: As of July, there were 373,000 job openings in the construction sector. While this is further proof of the positive outlook for the industry, it may not be entirely good news for builders. According to a recent L.E.K. Consulting Construction Survey, more than 40% of residential contractors are facing some degree of labor shortage. And it’s causing serious issues for contractors’ and homeowners’ bottom lines. According to a National Association of Home Builders (NAHB) survey, the labor shortage has led contractors and builders to raise home prices, delay projects and even turn down potential projects (see Figure 1).
The long-term prognosis for the construction labor pool is worrisome for two particular reasons. First, the average age of construction workers has increased over the past 15 years as baby boomers progress through the life cycle. According to AARP, upward of 10,000 baby boomers reach retirement age each day. Second, given dwindling interest in the industry from workers below age 25, the lack of trade workers to fill those vacancies could prove challenging (see Figure 2).
Uncertainty around current U.S. immigration policies portends a strain on hiring as well. Immigrant workers comprise a large percentage of the construction industry workforce, increasing from 20% in 2004 to 25% in 2016.1 With immigration policies in flux, the construction workforce may get further squeezed, as more than 100,000 U.S. construction workers are at risk of deportation.
How are contractors attempting to turn things around? They’ve increased construction wages to attract and retain workers, especially in residential construction, which has grown at a faster rate than private industries overall (see Figure 3). But increasing payroll hits contractors’ bottom lines and subsequently affects how much homeowners, investors and businesses are paying for construction projects.
Are higher wages, better recruitment efforts and employee training enough to stem the tide? Maybe not. Time- and labor-saving products — not necessarily more people — may be the key to mitigating the current labor crisis. Looking ahead, innovations that companies adopt over time to reduce labor can increase productivity and deliver value to the customer, which has lasting impact regardless of the labor market.
In the following sections, we examine some products that make installation projects simpler and faster or that combine multiple products — and sometimes steps — into one. In addition, we highlight products that are reducing the need for highly skilled labor through streamlined installation processes or advanced technology, opening up a larger pool of available workers to fill the open jobs.
Flooring installation and roofing jobs are typically lengthy, laborious processes. However, products are popping up on the market that promise to make these tasks quicker and easier.
One such product is LifeProof, a luxury vinyl flooring product that has experienced considerable growth following its national rollout at Home Depot. Touted as a faster, simpler alternative to ceramic tile, it has built-in waterproofing that enables it to be installed directly over the subfloor or existing flooring, eliminating the need for a separate underlayment or membrane.
Another example is prefabricated roof trusses, which can reduce roof installation time to as little as a day. In a survey conducted by Home Innovation Research Labs, 17% of builders indicated that they would be likely to use roof trusses more often in the coming year, a sign of shifting attitudes toward precut framing packages.
From slow-growing mold to an unforeseen natural disaster, water has the potential to do real harm, making weatherization and waterproofing a critical step in any building project. It also typically eats up time, requires multiple steps and takes a skilled hand. However, innovative companies are replacing traditional methods and materials and taking a less-is-more approach.
For instance, weatherization of a structure typically calls for “housewrap,” a time-consuming, multistep process. The Huber ZIP System integrates a structural roof and wall system with a water- and air-resistant barrier, turning weatherization into a simple two-step process. According to Home Innovation Research Labs, the ZIP System is 40% faster than using housewrap. It’s no surprise, then, that the ZIP System has showed continued growth in recent years and now represents ~11% of all wall sheathing installed in new home construction. Moreover, in the 2018 Hanley Wood Builder Brand Use Study, the ZIP System ranked as the most used exterior wall sheathing brand.
In addition, the DensElement Barrier System and USG Tremco Air Barrier System have eliminated the process of applying membranes and building wraps over sheathing as part of the building envelope system. Instead, those elements have been built directly into the sheathing product to reduce steps and decrease installation time.
Contractors can now hire less-skilled workers to complete tasks that may have been handled exclusively by skilled workers in the past, thanks to some recent product innovations. One-piece, pre-sloped shower systems are a good example of one such innovation.
While shower pans are typically installed through layering the bed and membrane, Tile Redi has developed and commercialized premolded, one-piece urethane shower pans that can be placed directly into the shower and serve as the substrate for tile to be installed. This product has gained traction with companies such as hotel chains that want a consistent final product and fast installation. Similarly, Marmite and other companies offer a high-quality engineered stone shower tray, which provides strong aesthetics and durability while reducing or eliminating the need for an expensive and sometimes hard to schedule tiling contractor for the shower.
On a larger scale, modular/off-site building solutions have become more relevant. More than half of construction firms used prefabricated assemblies for at least 20% of their project work in 2016, compared with 26% of companies in 2010. By centralizing many of the production steps in a controlled prefab facility, builders can more effectively and efficiently utilize their workforce by eliminating the travel between work sites and keeping them working throughout difficult weather periods. This can result in improved productivity, with each specialty contractor able to finish more work in a given day.
In addition to the labor savings, modular construction can shorten project schedules by allowing fabrication, assembly and testing to be completed at the same time as any site preparation or facility work. This can cut down the time until the building is ready for occupancy by 30%-50% relative to traditional construction. For example, Marriott recently announced plans to build a 26-story, 168-room hotel in just 90 days, with the fully outfitted rooms being prefabricated in a factory in Poland.
The construction industry has entered the 21st century: Some 22% of construction firms surveyed by ACG of America reported an increase in the use of labor-saving equipment, tools and machinery, such as drones, robots, GPS and laser-guided machinery.
Some of those firms may have worked with EagleView, a company that uses drones to survey residential and commercial structures for roof measurements and other information needed by roofing contractors. It eliminates the time-consuming human process of climbing onto the roof to take measurements and determine the job scope. In addition, the process ensures more accurate estimates and speeds up the workflow.
Unfortunately, the tightening U.S. construction labor market has made it difficult for builders and contractors to meet increasing demand. For building products manufacturers, however, the labor shortage has created tremendous opportunities for creativity and innovation. From one-piece showers to simplified waterproofing techniques to measurement-gathering drones, these solutions can offer relief to contractors and builders as they weather the storm. And according to L.E.K.’s recent Contractor Survey, these are products for which contractors are willing to pay a premium. Moreover, these innovations have a lasting effect, regardless of the labor market ― an effect that will increase productivity and provide value to the customer through cost and quality. So yes, the labor squeeze is here to stay. However, the age of labor- and time-saving innovation is here to stay, too. Companies that invest in research and development to drive product innovation to address these needs will win big in this tighter labor landscape, and beyond.
Endnote:
12016 American Community Survey data by the National Association of Home Builders’ Housing Economics