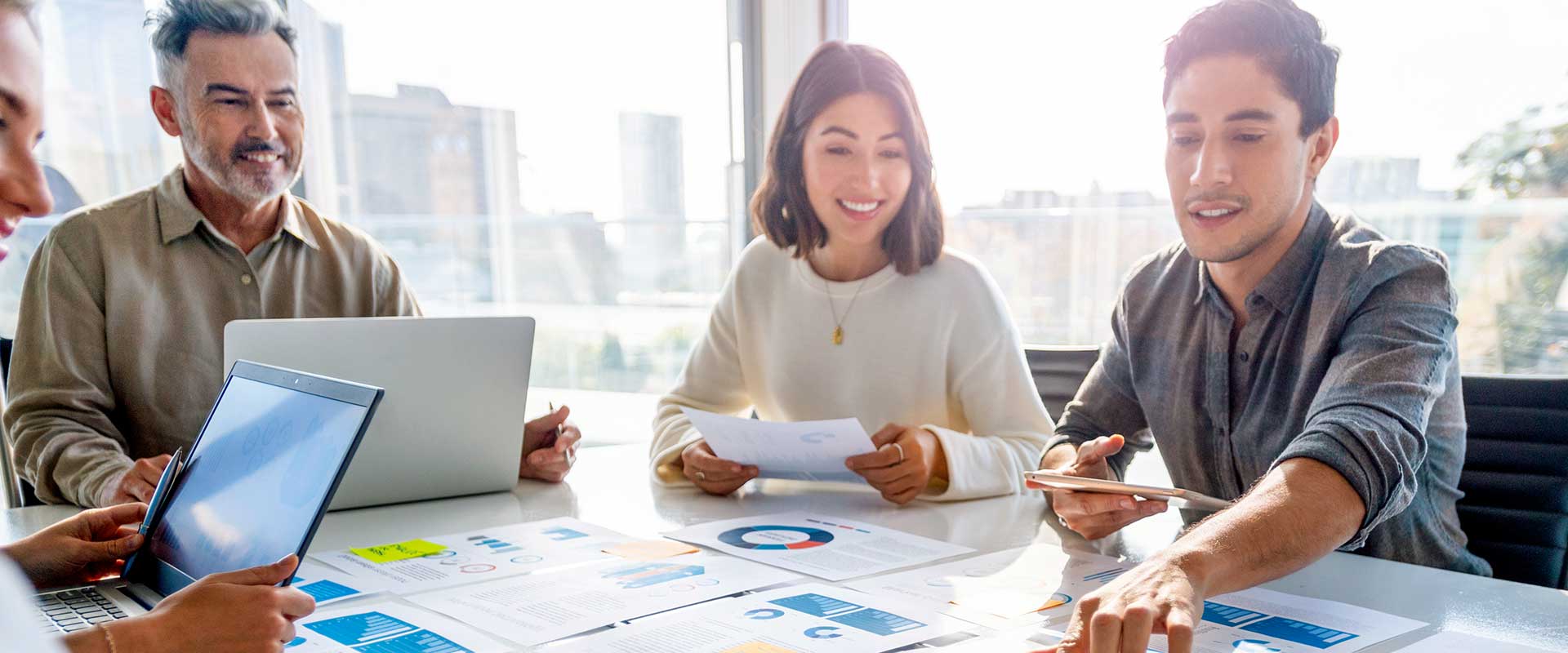
A leading pharmaceutical distributor saw a sharp decline in warehouse productivity after implementing a new Warehouse Management System (WMS). L.E.K. Consulting was engaged to evaluate warehouse performance and identify improvement opportunities. Through a comprehensive, four-facility assessment, L.E.K. uncovered a 17%-34% potential productivity uplift and designed a phased implementation plan to capture the gains and restore sustainable operations.
Challenge:
The company lagged industry benchmarks in warehousing performance, with declining efficiency further driving up labor costs.
New technology investments failed to deliver expected productivity gains, with labor instead increasing to handle operational disruptions.
Management was unclear on where to focus for maximum uplift and sought an outside-in assessment to identify and prioritize 4-wall improvement initiatives.
Approach:
Our team designed a rapid, hands-on 4-wall improvement program to identify operational challenges, develop efficiency uplift solutions and build a playbook for execution:
- Performance baselining: Analyzed distribution center operations by assessing key metrics (e.g., pick rates, pick exceptions, labor hours, inventory accuracy) and conducting detailed on-floor observations, interviews and time studies
- Root cause analysis and opportunity identification: Identified core issues inhibiting performance (e.g., high congestion in pick aisles), diagnosed root causes (e.g., fast turning items located too close together) and hypothesized improvement opportunities (e.g., revised velocity-based slotting strategy)
- Solution design and initiative development: Developed set of performance improvement initiatives based on identified issues and organized these into 5 solution themes for rollout to the full distribution network
- Implementation plan creation: Built a time-phased execution workplan, providing rollout guidance and target completion dates for each initiative
Results:
This hands-on assessment delivered actionable improvement opportunities that were initiated across the distributor’s network as a comprehensive performance improvement program. Collectively, this program enabled 17% labor reduction or capacity gain in one to two years, with 34% total uplift potential within three to five years.
Improvement opportunities were organized into five key solution areas:
- Staffing and labor Deployment: Develop weekly and intra-day labor planning tools to align near-term labor deployment with demand, minimizing idle time and wasted time from job transitions
- Equipment utilization: Adjust workflows and disseminate best practices for using automated retrieval and storage system to maximize machine utilization and achieve industry standard throughput rates
- Inventory control and slotting: Establish a consistent standard to track, measure and report inventory health across all facilities (e.g., inventory record defect rate) and right-size locations based on cubic velocity to reduce systematic inventory inaccuracies and eliminate associated productivity loss
- Workflow and waving strategy: Utilize waving rules and filtering to right-size waves based on volume, pick type and priority type, level-loading activity across the shift
- Layout improvement: Minimize narrow aisles for picking and arrange equipment to minimize walk time between functions
We defined 2 to 5 target initiatives within each of these key solution areas, each with corresponding execution guidelines. The improvement program was divided into three phases: the first six months focused on building foundational tools and processes, months 6-24 on gradually rolling out improvement initiatives and months 24+ on aggressively pursuing improvement targets.
Conclusion:
L.E.K.’s 4-wall DC improvement program disrupted the company’s status quo and established a clear path to reverse poor performance trends. If your business is looking to transform your warehousing operations, our Operations and Supply Chain team can help deliver similar impactful results.
Contact us to learn how we can drive sustainable improvements for your organization.
L.E.K. Consulting is a registered trademark of L.E.K. Consulting LLC. All other products and brands mentioned in this document are properties of their respective owners. © 2025 L.E.K. Consulting LLC
05282025150514