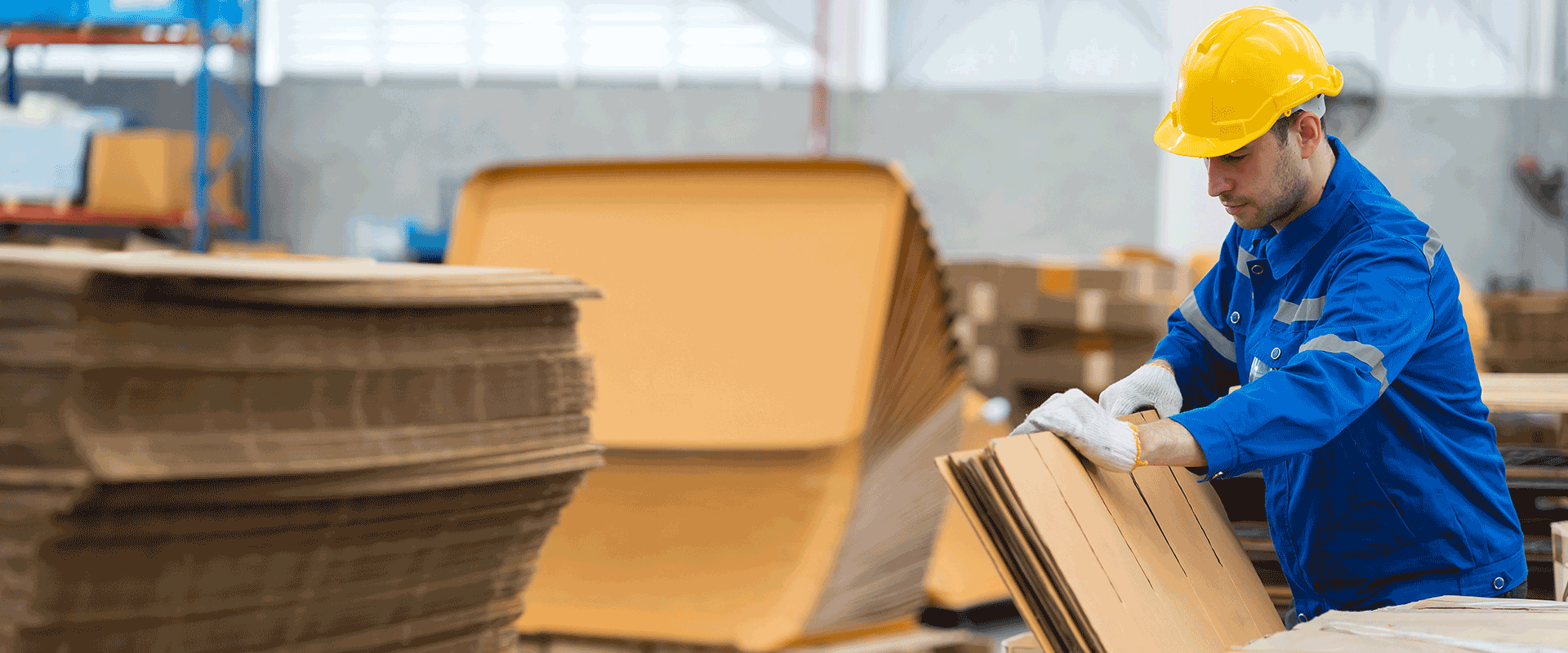
Health and Safety Concerns and a Bid for Greater Functionality Are Impacting Packaging Materials Inputs
- Article
A potent combination of growing consumer awareness and increasing regulatory pressure is causing a rise in demand for packaging inputs that enhance safety while eliminating toxic chemicals and by-products.
Meanwhile, as consumers seek packaging that is both convenient and easy to use and brands face pressure to differentiate themselves, finding solutions that extend the shelf life of food is becoming an ever-greater priority, all while ecommerce necessitates packaging that is not just more durable but can also be produced more efficiently.
Both developments have tangible ramifications for packaging manufacturers and converters — and, by extension, the chemicals and materials companies that supply them in the packaging value chain.
Not only are consumers becoming more educated about the potential health risks associated with packaging materials and the inputs that go into those materials, but regulations around chemicals used in packaging are becoming more stringent (e.g., banning per- and polyfluoroalkyl substances, aka PFAS, in food packaging). Extended producer responsibility policies are also increasingly holding brand owners who use packaging in their products responsible for the entire life cycle of those products, including the disposal of packaging chemical inputs, prompting companies to seek safer alternatives.
As a result, demand is increasing for packaging materials and inputs that enhance safety by eliminating certain chemicals and by-products and that provide similar levels of performance. Specific innovations in this field include water-based inks that eliminate the use of volatile organic compounds (VOCs), biopolymers that can replace phenol-based chemicals used as barrier coatings, and starch or acrylic adhesives that can replace more hazardous sodium-silicate adhesives.
Reduced VOCs (inks) — Unlike traditional solvent-based inks, which release harmful VOCs into the air during the drying process, water-based inks utilize water instead of solvent. Applications include printing on materials used for aseptic and fresh food packaging, paper cups, plates and food cartons, as well as those that are hygiene-specific.
Phenol-free materials (coatings) — Biopolymer coatings, which are derived from renewable resources like corn starch or sugarcane, are replacing phenol-based chemicals (such as PFAS) in food-contact packaging (e.g., containers, trays and to-go boxes), where they act as a barrier against moisture and grease.
Nontoxic, recyclable starch (adhesives) — Starch adhesives, which are used primarily in corrugated boxes, and acrylic adhesives, used with shipping labels, provide recyclable and nontoxic alternatives to more traditional sodium-silicate adhesives, which can irritate eyes and skin and have performance issues when wet or too dry.
Functionality is also driving the mix of packaging inputs more than ever before, with inputs that improve packaging performance increasingly in demand. It’s an opportunity that both chemicals and manufacturing companies in this space should embrace.
Packaging functionality starts with understanding the foundational “job” that the packaging is being asked to do. In some instances, for example, the packaging is critical to keeping products fresh and safe; in others, its primary functionality is to effectively convey the brand message and drive consumer shelf appeal.
Packaging functionality can also extend into operational efficiency in packaging conversion or printing, or when it comes to filling steps of the value chain. In these examples, helping increase production throughputs, yields and speed and minimizing production waste can be tangible value levers that accrue to packaging manufacturers, co-packers/co-fillers and brand owners.
Extending shelf life/reducing food waste (substrates) — “Active packaging” refers to packaging technologies designed to interact with the product or environment inside the package, such as oxygen absorbers or antimicrobial agents. Using active packaging not only reduces food spoilage but extends the shelf life of food to, ultimately, minimize food waste. It also makes food packaging more sustainable by removing the need for desiccant packs.
Applications include packaging for moisture-sensitive products, such as snacks, baked goods and pharmaceuticals, where maintaining an optimal humidity level is crucial for preventing spoilage and the growth of mold and mildew, which can compromise product quality.
Enhanced production efficiency (inks) — Ultraviolet (UV)-curable inks cure instantly under UV light, speeding up production by eliminating drying times and reducing emissions of VOCs. These inks also produce sharp, high-quality images with less ink spreading, which results in a higher-quality product.
Flexible packaging, labels and high-end product packaging for cosmetics are among the applications, as are those that need fast throughput and high print quality, such as pharmaceuticals and food products.
The above are but a few examples of the shifts in packaging material inputs that are occurring, either due to health and safety concerns or a desire for increased functionality. There are, of course, other factors also influencing the selection of packaging materials inputs. To that end, we’ve published a three-part series on the topic, including the macro trends in packaging and how corporate sustainability goals are increasingly impacting the mix of packaging inputs.
To set up a meeting to learn more, please contact us.
L.E.K. Consulting is a registered trademark of L.E.K. Consulting LLC. All other products and brands mentioned in this document are properties of their respective owners. © 2025 L.E.K. Consulting LLC